Transforming Operations in today’s dynamic realm of industrial manufacturing requires companies to embrace innovation that enhances efficiency, minimizes environmental impact, and safeguards workforce health.
This article unveils a comprehensive dust collection project undertaken by a leading Ontario pallet manufacturing company—an initiative that exemplifies transforming operations through modern engineering solutions. Utilizing cutting-edge technology, including advanced 3D computer modelling, the company successfully implemented a customized system tailored to its facility’s unique needs.
While maintaining client confidentiality, we delve into the strategic planning, execution, and long-term benefits of this game-changing initiative. From improved air quality to optimized plant layout, this project highlights the potential impact of smart dust management on productivity, compliance, and worker satisfaction—offering valuable insights for similar industries seeking sustainable upgrades.
Challenges in Pallet Manufacturing
Pallet manufacturing inherently generates dust and particulate matter, presenting challenges such as compromised air quality and potential health hazards for workers. Additionally, inefficient dust management can lead to increased machinery maintenance costs and reduced operational efficiency.
Transforming Operations: The Decision to Implement a Dust Collection Project
Recognizing the need for a holistic solution, the Ontario pallet manufacturing company invested in a state-of-the-art dust collection project. The primary objectives were to enhance air quality, improve operational efficiency, and contribute to a more sustainable manufacturing process.
Utilizing 3D Computer Modeling
A standout feature of this project was the utilization of advanced 3D computer modeling technology. This innovative approach allowed the company to create a virtual representation of its facility, facilitating a detailed analysis of airflow, dust generation points, and potential areas for improvement. The 3D modeling not only ensured precision in assessment but also served as a visual aid for stakeholders.
Customized System Design
Informed by insights from 3D modeling, the company collaborated with experts to design a tailored dust collection system. This system incorporated high-efficiency filters, strategically placed extraction points, and advanced monitoring mechanisms for optimal performance.
Integration of Smart Monitoring
To further elevate the system’s efficiency, smart monitoring technology was integrated. Real-time sensors and data analytics tools continuously monitored air quality, dust levels, and system performance. This allowed for proactive maintenance and provided valuable data for ongoing process optimization.
Benefits and Outcomes
The successful dust collection project delivered substantial benefits for the Ontario pallet manufacturing company:
- Improved Air Quality: The new system effectively reduced airborne dust particles, fostering a healthier and safer working environment for employees.
- Enhanced Operational Efficiency: The streamlined dust management system led to reduced machine downtime and lower maintenance costs.
- Environmental Sustainability: The adoption of advanced dust collection technology aligned with the company’s commitment to sustainability, minimizing its environmental impact.
- Cost Savings: The initial investment proved financially prudent, resulting in long-term savings through improved equipment reliability and reduced maintenance expenses.
Conclusion
The Ontario pallet manufacturing company’s dust collection project exemplifies how technological innovation plays a crucial role in transforming operations to meet modern industrial demands.
Through 3D computer modelling, smart monitoring, and a tailored approach, the company not only improved operational efficiency but also demonstrated a deep commitment to workforce well-being and environmental sustainability. This initiative stands as a practical model for transforming operations in facilities that face similar air quality and compliance challenges.
By investing in advanced systems and forward-thinking design, the company reinforced its role as a leader in transforming operations within the manufacturing sector. As industries continue to evolve in response to regulatory pressures, climate goals, and economic demands, projects like this serve as beacons for others seeking innovative, long-term solutions.
Ultimately, transforming operations through strategic upgrades is not just about efficiency—it’s about creating safer workplaces, cleaner environments, and stronger futures for both businesses and their communities.
Interested in our Dust Collecting Options? Check them out here.
Dust Collector Project Draw
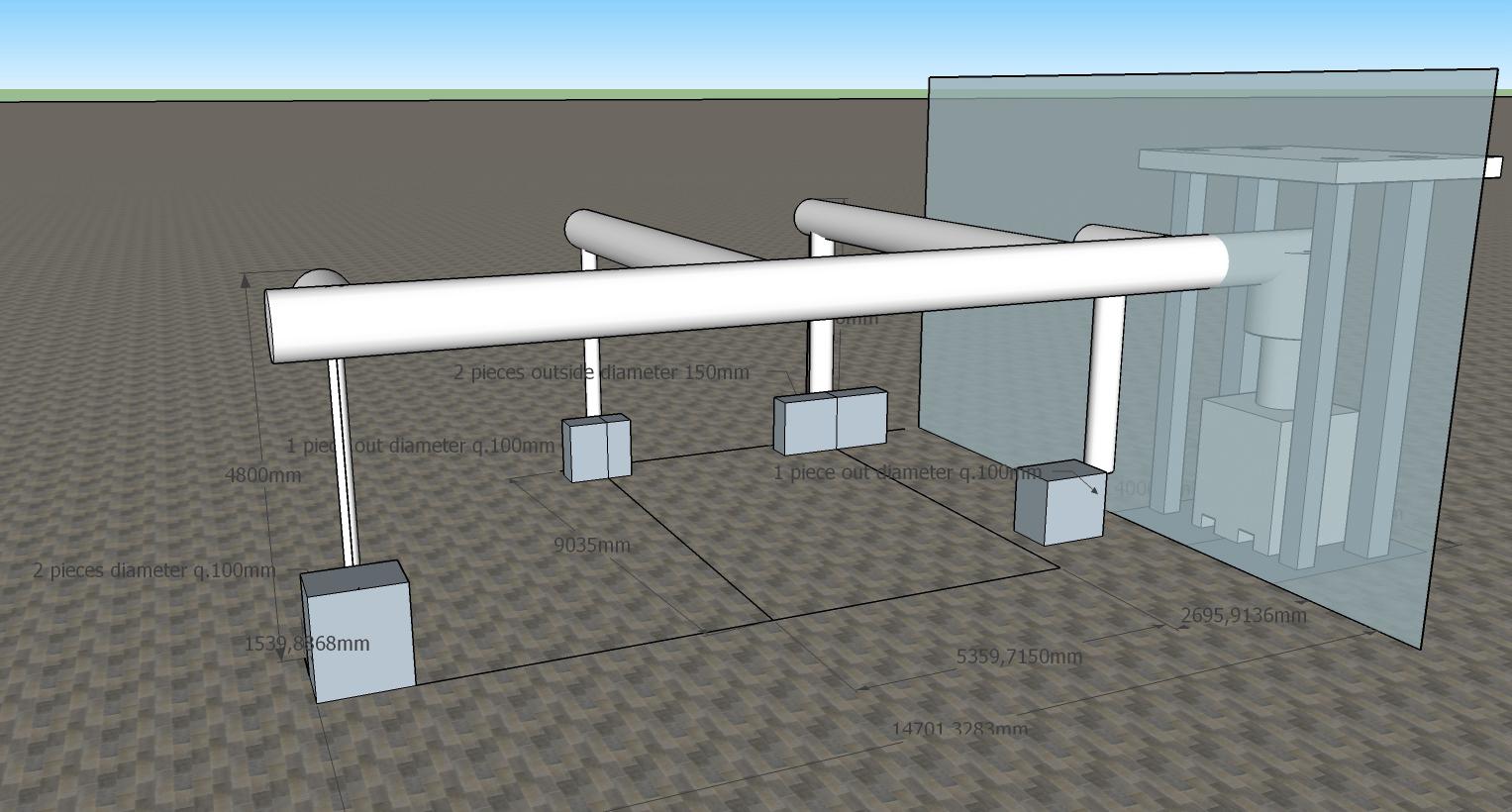
Dust Collector Project Draw
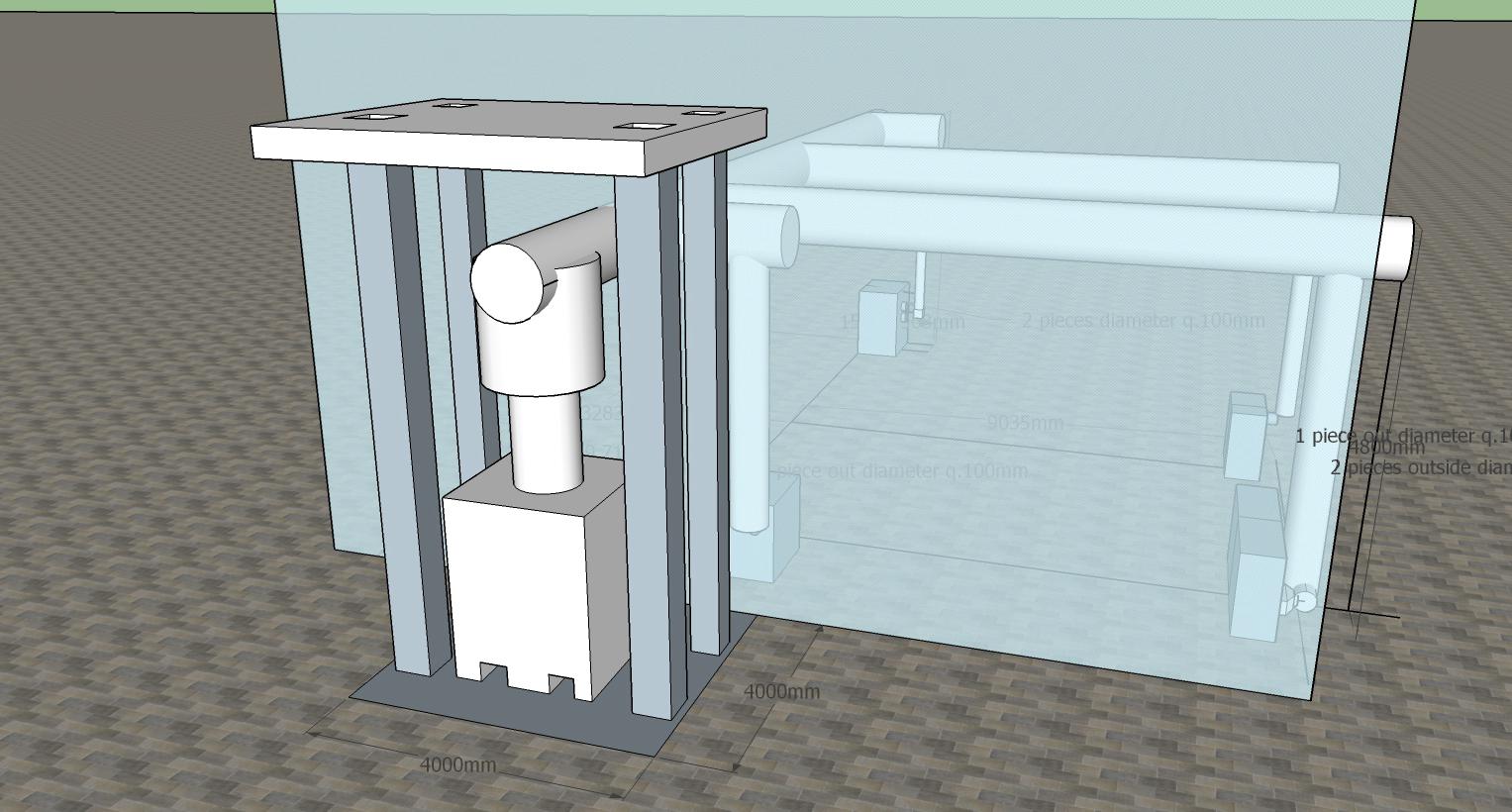
Dust Collector Project Draw CANADA