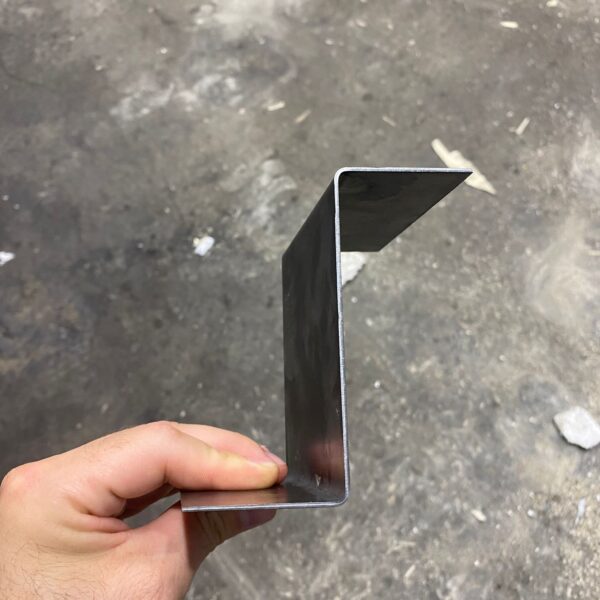
A full serve electric press brake offers a range of advantages over traditional hydraulic press brakes, making it an excellent investment for any metalworking operation. These machines use an electric servo motor to power the ram, providing precise and efficient bending capabilities. Here are some of the key advantages of using a full serve electric press brake.
Dener machine is a leading company in tueky for the electrical press brake lines.
Increased Precision where you work on precise metal or aircraft
Electric press brakes offer a higher degree of accuracy compared to hydraulic models. The use of an electric servo motor provides precise control over the bending angle and speed, resulting in more accurate bends with minimal errors.Electric press brakes have a faster cycle time compared to hydraulic models, allowing for faster production rates and increased efficiency. The rapid approach and return speeds of the electric motor reduce idle time, resulting in a more productive machine.
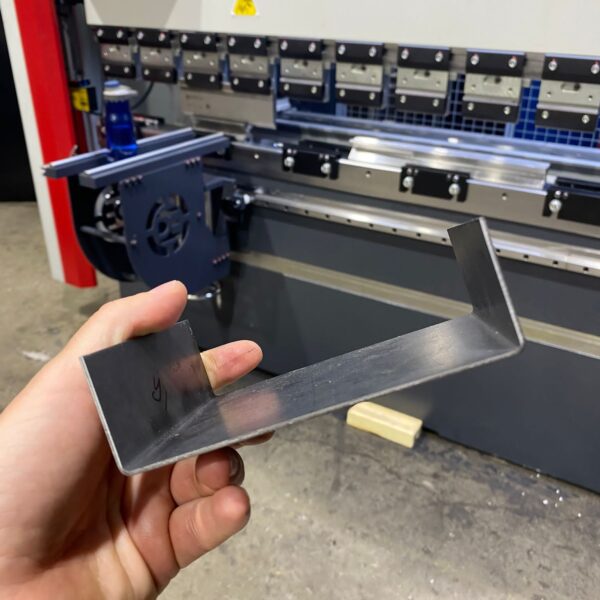
Increasing hydro bills
Electric press brakes consume less energy compared to hydraulic models, resulting in lower operating costs. The electric motor only uses energy when in operation, unlike hydraulic models that constantly consume energy to maintain hydraulic pressure adding up with overhead cost of operation a metal show plus the maintenance all adds up. Less Maintenance: Electric press brakes require less maintenance compared to hydraulic models. They have fewer components that need to be serviced, resulting in less downtime and lower maintenance costs over time.Quieter Operation: Electric press brakes are much quieter compared to hydraulic models. The electric motor operates silently, providing a quieter working environment for the operator and reducing noise pollution in the workplace.
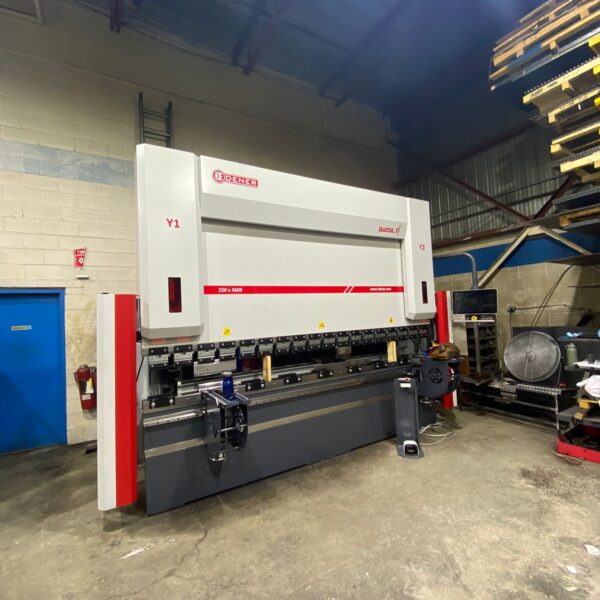
advantages of Full electric press brake
A full electric press brake offers several advantages over traditional hydraulic press brakes, including:
- Energy efficiency: Full electric press brakes consume significantly less energy than hydraulic press brakes, as they do not require a hydraulic oil pump or cooling system.
- Speed and accuracy: Full electric press brakes are faster and more accurate than hydraulic press brakes, thanks to their precise and consistent movements. This can lead to increased productivity and higher-quality bends.
- Low maintenance: Full electric press brakes have fewer moving parts and require less maintenance than hydraulic press brakes, reducing downtime and maintenance costs.
- Noise reduction: Full electric press brakes are quieter than hydraulic press brakes, making them a better choice for noise-sensitive environments.
- Safety: Full electric press brakes have advanced safety features, including light curtains and interlocks, which help prevent accidents and ensure operator safety.
What is a full electric press brake machine ?
A full electric press brake is a type of press brake that uses electric motors and drives to power its movements, rather than hydraulic systems. This means that it does not require any hydraulic oil or hydraulic pump, resulting in a more energy-efficient and environmentally-friendly solution.
The movements of a full electric press brake are controlled by a computer numerical control (CNC) system, which allows for precise and repeatable bending operations. The CNC system also provides real-time monitoring and adjustment of the bending process, ensuring accuracy and consistency.
Full electric press brakes are known for their speed, accuracy, and low maintenance requirements. They also tend to be quieter and safer than hydraulic press brakes, due to the absence of hydraulic oil and the advanced safety features that are often incorporated into their design.
Overall, a full electric press brake is a highly advanced and efficient solution for metal bending and forming operations, especially for those looking to reduce their energy consumption and environmental impact.
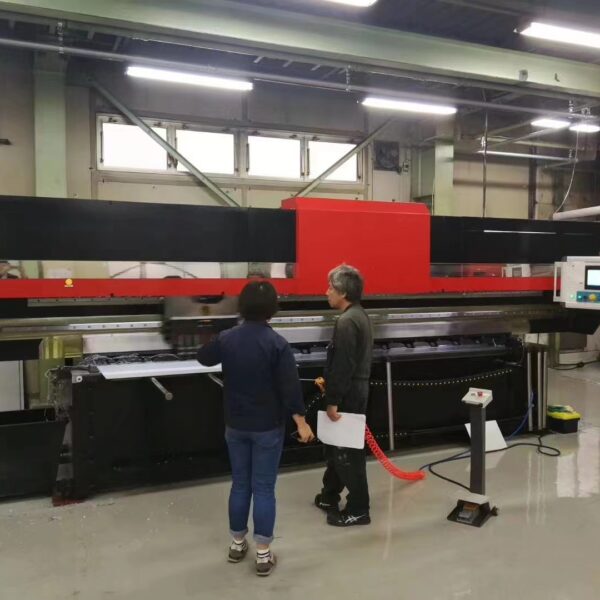
how should I choose the right press brake machine ?
Choosing the right press brake for your metal forming operations is critical to achieving high-quality results and maximizing your productivity. Here are some key factors to consider when selecting a press brake:
- Bending capacity: The first and most important consideration is the maximum bending capacity required for your application. This will depend on the thickness and type of material you need to bend, as well as the required length of the bend.
- Accuracy and repeatability: Look for a press brake with a CNC control system that provides high precision and repeatability, especially if you need to produce complex parts or repeat the same bending operations over time.
- Speed: Consider the speed of the press brake, especially if you have high-volume production requirements. A faster machine can help increase your productivity and reduce your overall production time.
- Safety features: Safety should always be a top priority when choosing a press brake. Look for a machine with advanced safety features such as interlocks, light curtains, and guards to protect operators from accidents and ensure compliance with safety regulations.
- Maintenance requirements: Consider the maintenance requirements of the press brake, including the frequency and complexity of maintenance tasks, as well as the availability and cost of replacement parts.
- Price and value: Finally, consider the price of the press brake and the value it provides for your operations. Look for a machine that offers a good balance of features, performance, and price, and that is backed by a reputable manufacturer with good customer support and service.
By considering these factors, you can choose the right press brake that meets your specific needs and requirements, and that provides a high-quality and reliable solution for your metal forming operations.
Please contact to your press brake specialist for more questions